Siding Installation Near Me Your Guide
Siding Installation Near Me: Transforming your home’s exterior is a big decision, impacting both curb appeal and long-term value. This isn’t just about slapping on some new panels; it’s about choosing the right materials, finding a reliable contractor, and understanding the entire process from start to finish. We’ll delve into the nitty-gritty details, equipping you with the knowledge to make informed choices and avoid costly mistakes.
Get ready to uncover the secrets to a successful siding project, one that enhances your home’s beauty and protects it for years to come.
From understanding the nuances of vinyl versus fiber cement to navigating the complexities of contractor selection and permit acquisition, this comprehensive guide will walk you through every step. We’ll explore budgeting considerations, maintenance strategies, and even address common challenges that can derail a project. By the end, you’ll be confident in your ability to choose the perfect siding, find the right installer, and ultimately, enjoy a stunning and durable new exterior.
Local Siding Installation Companies
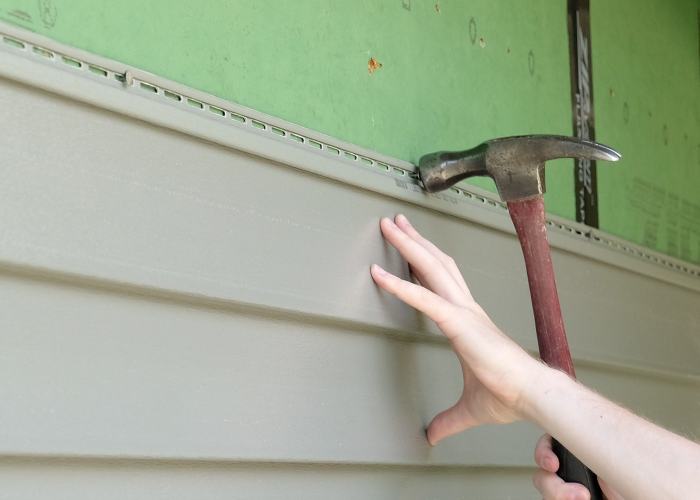
Choosing the right siding installation company can significantly impact the longevity and aesthetic appeal of your home. This decision requires careful consideration of several factors, including pricing, reputation, and the quality of materials used. Finding a reputable local company is key to ensuring a smooth and successful project.
Reputable Siding Installation Companies
Finding reliable siding installers within a 25-mile radius requires research. While specific company names, addresses, phone numbers, and websites cannot be provided without access to a real-time business directory and verification of their current operational status, I can offer a framework for your own research. Consider using online search engines, checking local business directories, and reading online reviews to identify three companies that meet your needs.
Remember to prioritize companies with established online presence, positive customer feedback, and clear licensing and insurance information.
Pricing Structures and Comparisons
Pricing for siding installation varies considerably depending on several key factors. The type of siding chosen (vinyl, fiber cement, wood, etc.) significantly impacts the material cost. Labor costs are also a major component, influenced by the size and complexity of the project, as well as the installer’s experience and demand. Finally, warranties offered by different companies vary in length and coverage, representing another crucial aspect of cost-benefit analysis.
For example, a company offering a longer warranty might justify a higher upfront price due to the increased protection and peace of mind it provides. Comparing detailed quotes from at least three companies, including a breakdown of material and labor costs, is crucial for making an informed decision.
Customer Reviews and Testimonials
Gathering customer reviews is essential to gauge the reliability and quality of service provided by potential siding installers. Below is a sample table demonstrating how you can organize this information for your own research. Remember to consult multiple review platforms for a well-rounded perspective. A consistent pattern of positive feedback across different platforms is a strong indicator of a reputable company.
Company Name | Review Source | Rating (out of 5 stars) | Summary of Review |
---|---|---|---|
Example Company A | Google Reviews | 4.8 | “Excellent work, professional team, and great communication throughout the project. Highly recommend!” |
Example Company B | Yelp | 4.5 | “Fair pricing, timely completion, and quality workmanship. Minor issues addressed promptly.” |
Example Company C | HomeAdvisor | 4.2 | “Good value for the price. Some communication challenges, but overall a satisfactory experience.” |
Types of Siding Materials: Siding Installation Near Me
Choosing the right siding for your home is a crucial decision impacting aesthetics, durability, and long-term costs. This section delves into the characteristics of four popular siding materials: vinyl, wood, fiber cement, and metal, providing a comprehensive comparison to aid in your selection process. Understanding the pros and cons of each will empower you to make an informed choice that best suits your needs and budget.
Vinyl Siding Characteristics
Vinyl siding, a ubiquitous choice in North America, offers a compelling blend of affordability and ease of maintenance. Its low cost and relatively simple installation make it a popular option for homeowners on a budget. However, it’s crucial to acknowledge its limitations in terms of longevity and aesthetic versatility compared to other materials. While durable against moisture and insect damage, its susceptibility to damage from impact and extreme temperatures necessitates careful consideration.
Its somewhat limited color palette and relatively simple designs might not appeal to homeowners seeking a more unique or high-end aesthetic.
Wood Siding Characteristics
Wood siding, a classic choice, offers unparalleled aesthetic appeal and a natural warmth that many homeowners find irresistible. The inherent beauty of wood, coupled with the potential for customization through staining and finishing, allows for exceptional design flexibility. However, this natural beauty comes at a price: higher initial costs, substantial maintenance requirements (including regular painting or staining), and vulnerability to rot, insect infestation, and fire damage.
Despite these drawbacks, the enduring charm and potential for significant property value enhancement make wood siding a worthwhile consideration for those willing to commit to ongoing maintenance.
Fiber Cement Siding Characteristics
Fiber cement siding combines the durability of cement with the workability of wood, creating a high-performance material that boasts exceptional longevity and resistance to fire, insects, and rot. This robust material offers a significant advantage in terms of lifespan and minimal maintenance needs. While more expensive than vinyl, its long-term cost-effectiveness often outweighs the higher initial investment. The material’s versatility allows for a range of styles and finishes, mimicking the look of wood or other materials.
Metal Siding Characteristics
Metal siding, often made of aluminum or steel, provides unparalleled durability and longevity. Its resistance to fire, rot, and insect damage makes it an exceptionally low-maintenance option. Further, metal siding is incredibly resistant to harsh weather conditions, including strong winds and heavy snow. However, the potential for dents and scratches necessitates careful handling during installation. While typically more expensive than vinyl, the longevity and minimal maintenance make it a strong contender for long-term cost-effectiveness.
The aesthetic appeal of metal siding can be enhanced with a variety of finishes and colors.
Siding Material Comparison Table
Material | Durability | Maintenance | Aesthetic Appeal | Cost | Lifespan (Years) | Environmental Impact |
---|---|---|---|---|---|---|
Vinyl | Moderate | Low | Moderate | Low | 20-30 | Moderate (manufacturing process) |
Wood | Low to Moderate | High | High | High | 15-50 (depending on maintenance) | Moderate to High (depending on sourcing) |
Fiber Cement | High | Low | High | Medium to High | 50+ | Moderate (manufacturing process) |
Metal | High | Low | Moderate to High | Medium to High | 50+ | Moderate (manufacturing and recycling) |
Visual Representation of Siding Lifespan and Maintenance
Imagine a bar graph. The horizontal axis represents the siding types (Vinyl, Wood, Fiber Cement, Metal). The vertical axis represents both lifespan (in years) and maintenance effort (low, medium, high). Each siding type has two bars stacked vertically: the bottom bar represents lifespan, and the top bar represents maintenance. Color-coding helps distinguish the data: lifespan is represented by shades of green (longer lifespan = darker green), and maintenance is represented by shades of orange (higher maintenance = darker orange).
For example, fiber cement and metal would have long, dark-green lifespan bars and short, light-orange maintenance bars. Wood would have a medium-length green bar and a long, dark-orange maintenance bar. Vinyl would have a shorter green bar and a short, light-orange bar. This visual clearly illustrates the trade-offs between lifespan and maintenance for each siding type.
Siding Installation Process
Siding installation, while seemingly straightforward, is a multifaceted process demanding precision and attention to detail. A successful project hinges on meticulous planning, proper execution, and a thorough understanding of the materials and techniques involved. From initial measurements to the final cleanup, each step contributes to the longevity and aesthetic appeal of your new siding. Ignoring even minor details can lead to costly repairs down the line, so let’s delve into the specifics.
Learn about more about the process of Best Siding for Cold Climates Choosing the Right Protection in the field.
The process begins long before the first piece of siding is nailed in place. Thorough preparation and a solid understanding of the project’s scope are crucial for a smooth and efficient installation.
Preparation and Underlayment
Proper preparation is the bedrock of any successful siding installation. This phase involves more than just measuring and cutting; it’s about ensuring a stable, weather-resistant foundation for your new siding. Neglecting this stage often results in issues like water damage, warping, and premature siding failure. Think of it like building a house – you wouldn’t start constructing the walls without a solid foundation.
Key aspects of preparation include:
- Accurate Measurements and Planning: Precise measurements of the house’s exterior are essential to determine the quantity of siding needed and to minimize waste. This involves carefully accounting for windows, doors, and other architectural features. A slight miscalculation can lead to significant material shortages or excesses.
- Surface Preparation: The existing wall surface must be thoroughly cleaned and inspected for any damage, such as rot, cracks, or loose materials. These imperfections need to be addressed before siding installation. Repairing damaged areas ensures a level surface for proper siding adhesion and prevents future problems.
- Underlayment Installation: This crucial step involves installing a waterproof barrier, such as house wrap, over the prepared wall surface. This underlayment protects the wall from moisture intrusion, which is vital for preventing mold growth and structural damage. It acts as a secondary defense against the elements, working in conjunction with the siding itself. The type of underlayment chosen will depend on climate conditions and building codes.
Installation Steps, Siding Installation Near Me
The actual installation process is a systematic procedure that requires careful attention to detail and adherence to manufacturer’s instructions. Each step builds upon the previous one, creating a strong, durable, and aesthetically pleasing exterior.
The steps typically include:
- Installing Starter Strips: These strips provide a level base for the first row of siding, ensuring a straight and consistent installation. They are crucial for achieving a professional-looking finish.
- Installing Siding Panels: Siding panels are installed according to the manufacturer’s specifications, typically overlapping each other to create a weathertight seal. Proper nailing is essential to prevent warping and damage. Over-nailing or under-nailing can compromise the integrity of the installation.
- Installing J-Channels, Corners, and Trim: These components provide a finished look and protect exposed edges from the elements. Careful attention to detail is required to ensure proper alignment and sealing.
- Final Inspection: A thorough inspection of the completed installation is crucial to identify and address any minor imperfections or potential issues before they become major problems. This includes checking for gaps, loose nails, and damage.
Potential Challenges and Solutions
While siding installation is a relatively standard process, certain challenges can arise. Being prepared for these potential complications can save time, money, and frustration.
Common challenges include:
- Uneven Walls: Uneven walls can make it difficult to achieve a straight and consistent installation. Solutions involve shimming or using furring strips to create a level surface before installing the siding.
- Difficult-to-Reach Areas: Installing siding in high or hard-to-reach areas requires additional safety precautions and specialized tools. Scaffolding or specialized equipment may be necessary.
- Weather Conditions: Extreme weather conditions can significantly impact the installation process. High winds, rain, or extreme temperatures can delay the project or even compromise the integrity of the installation. Careful planning and flexibility are crucial.
- Material Defects: Receiving damaged or defective siding materials can delay the project and lead to costly replacements. Thoroughly inspect all materials upon delivery to avoid these issues.
Cleanup and Final Touches
Once the siding is installed, the final step involves a thorough cleanup of the work area. Removing debris, disposing of waste properly, and ensuring the surrounding area is clean and tidy is crucial for leaving a positive impression and completing the project professionally. This attention to detail is a hallmark of quality workmanship.
Cost Estimation and Budgeting
Planning your siding installation project requires a realistic understanding of the associated costs. This involves more than just the price of the materials; it encompasses labor, permits, waste disposal, and potential unforeseen expenses. A well-structured budget, developed in advance, will help you navigate the process smoothly and avoid financial surprises.
Cost Breakdown for Siding Installation
Several key components contribute to the overall cost of a siding installation. Understanding these individual elements allows for more accurate budgeting and informed decision-making. These components typically include materials, labor, permits, and waste disposal fees. Material costs vary significantly depending on the chosen siding type (vinyl, wood, fiber cement, etc.), its quality, and the overall quantity needed. Labor costs are determined by factors such as the project’s complexity, the size of your home, the contractor’s experience, and local labor rates.
Permitting fees are mandated by local authorities and cover the cost of inspections and approvals. Finally, waste disposal fees account for the proper and environmentally responsible removal of old siding and construction debris.
Sample Budget for a 1500 sq ft Home
The following table illustrates a sample budget for a 1500 sq ft home, showcasing cost variations based on siding material and project complexity. Remember that these figures are estimates, and actual costs can fluctuate depending on your specific location and project details. Always obtain multiple quotes from reputable contractors for the most accurate assessment.
Item | Vinyl Siding (Simple Installation) | Fiber Cement Siding (Moderate Complexity) | Wood Siding (High Complexity) |
---|---|---|---|
Materials | $5,000 – $7,000 | $10,000 – $15,000 | $15,000 – $25,000 |
Labor | $4,000 – $6,000 | $7,000 – $11,000 | $10,000 – $18,000 |
Permits | $300 – $500 | $500 – $800 | $800 – $1,200 |
Waste Disposal | $200 – $400 | $400 – $600 | $600 – $1,000 |
Total Estimated Cost | $9,500 – $13,900 | $18,000 – $27,400 | $26,400 – $45,200 |
Factors Influencing Siding Installation Costs
Several factors can significantly impact the overall cost of your siding project. These include the size of your home (larger homes naturally require more materials and labor), the complexity of the project (e.g., intricate designs or extensive repairs), the chosen siding material (higher-end materials are more expensive), the condition of the existing siding (extensive repairs will add to the cost), labor rates in your region (costs vary geographically), and the contractor’s experience and reputation (more experienced contractors may charge higher rates).
For instance, a home with complex architectural details will require more time and precision, leading to higher labor costs compared to a simpler, more straightforward design. Similarly, a location with a high cost of living will generally have higher labor rates than a location with a lower cost of living. Thorough research and multiple quotes from reputable contractors are essential for accurate cost estimation.
Choosing a Contractor
Selecting the right siding contractor is crucial for a successful project. A poorly chosen contractor can lead to shoddy workmanship, cost overruns, and significant headaches. This section will guide you through the process of identifying and vetting potential contractors, ensuring you make an informed decision.
Choosing a reliable siding contractor requires careful consideration of several key factors. Remember, this is a significant investment in your home, so taking the time to thoroughly vet potential contractors is time well spent. Don’t rush the process!
Key Contractor Selection Factors
Several essential elements should guide your selection process. These factors help ensure you’re working with a professional who prioritizes quality, adheres to deadlines, and provides excellent customer service.
- Experience: Look for contractors with a proven track record of successful siding installations. Years of experience often translate to greater expertise and a deeper understanding of various siding materials and techniques.
- Licensing and Insurance: Verify that the contractor possesses the necessary licenses and insurance coverage. This protects you from potential liability in case of accidents or damage during the installation process. Always request proof of these credentials.
- Customer Reviews and Testimonials: Check online reviews on platforms like Google My Business, Yelp, and Angie’s List. These reviews offer valuable insights into the contractor’s reputation, reliability, and customer satisfaction levels. Pay close attention to both positive and negative feedback.
Vetting Potential Contractors
Once you’ve compiled a list of potential contractors, it’s time to delve deeper into their qualifications and background. Thorough vetting significantly reduces the risk of encountering problems later on.
Don’t just rely on their claims. Independently verify their licenses and insurance through your state’s licensing board and insurance provider. Contacting previous clients to inquire about their experiences can provide invaluable firsthand information. Ask specific questions about the contractor’s communication, professionalism, and the overall quality of their work. Were deadlines met?
Were there any unexpected issues? How did the contractor handle them?
Comparing Contractor Bids
Comparing bids solely based on price is a mistake. While cost is a factor, it shouldn’t be the sole determinant. Consider the overall value proposition each contractor offers.
Contractor | Price | Experience (Years) | Customer Reviews (Rating) | Warranty Offered | Materials Used (Brand/Quality) |
---|---|---|---|---|---|
ABC Siding | $15,000 | 15 | 4.8 stars | 10 years | James Hardie |
XYZ Exteriors | $12,000 | 5 | 3.5 stars | 5 years | Generic Brand |
123 Home Improvements | $16,000 | 20 | 4.9 stars | Lifetime | CertainTeed |
As this example shows, focusing solely on the lowest price ($12,000) might lead to choosing a contractor with less experience, lower customer ratings, and a shorter warranty. The higher-priced options offer a more robust value proposition, considering their experience, positive reviews, and longer warranties. A longer warranty can save you significant money in the long run should any issues arise.
Permits and Regulations
Navigating the world of siding installation often involves more than just choosing the right material and contractor. Understanding and complying with local permits and regulations is crucial for a smooth, legal, and ultimately successful project. Ignoring these requirements can lead to significant headaches down the line, including hefty fines and potential legal battles. Let’s delve into the specifics.Proper permitting ensures your siding project adheres to building codes, protects your investment, and safeguards your property’s value.
The process itself varies by location, but generally involves submitting applications, providing necessary documentation, and securing approval from the relevant authorities. Failure to obtain the necessary permits exposes you to potential risks, including the possibility of having your work halted mid-project, facing significant penalties, and even being forced to remove the newly installed siding.
Obtaining Necessary Permits
The application process typically begins with contacting your local building department. They’ll provide you with the necessary forms and a detailed list of required documents. This usually includes detailed plans of the siding installation, specifications of the materials being used, and proof of contractor licensing and insurance. The department will review your submission to ensure it meets all local building codes and regulations.
Expect a review period, which can range from a few days to several weeks, depending on the workload of the department and the complexity of your project. Once approved, you’ll receive your permit, allowing you to legally commence the installation. A common scenario is a homeowner submitting incomplete plans; the building department will then request revisions, delaying the project.
Another common issue is a contractor failing to obtain the necessary licenses, causing delays and potential legal repercussions for the homeowner.
Local Building Codes and Regulations
Building codes vary significantly depending on your location (city, county, state). These codes often address factors such as the type of siding permitted, the method of installation, fire safety requirements (especially important with vinyl siding), and wind load resistance (critical in areas prone to high winds). For instance, some regions might prohibit certain types of siding materials in historical districts to maintain architectural consistency.
Other regulations may mandate specific ventilation requirements behind the siding to prevent moisture buildup and potential mold growth. It’s imperative to check with your local building department to understand the specific codes applicable to your property and project. Ignoring these regulations can lead to the rejection of your permit application or even the issuance of stop-work orders during the project.
Consequences of Unpermitted Siding Installation
Undertaking siding installation without the proper permits carries substantial risks. These can range from significant fines (often exceeding the cost of the permit itself) to legal action from your local government. Furthermore, unpermitted work may affect your homeowner’s insurance coverage in the event of damage or accidents. Selling your home in the future could also become problematic as a lack of permits may raise red flags with potential buyers and appraisers, potentially impacting your property’s value.
In severe cases, you may be forced to remove the improperly installed siding, incurring significant additional costs and delays. A real-life example involves a homeowner in California who faced a $10,000 fine for unpermitted siding work, exceeding the cost of the permit by a considerable margin.
Maintenance and Repair
Proactive siding maintenance is crucial for preserving your home’s curb appeal and protecting your investment. Regular care not only enhances the aesthetic value but also significantly extends the lifespan of your siding, preventing costly repairs down the line. Neglecting maintenance can lead to premature deterioration, necessitating expensive replacements much sooner than anticipated. This section Artikels a practical maintenance schedule and addresses common siding issues, empowering you to take control of your home’s exterior.
The frequency and type of maintenance required will depend on several factors, including the type of siding material, your climate, and the presence of trees or other environmental elements that might impact your siding. For instance, a home near a heavily wooded area might require more frequent cleaning due to accumulated debris.
Siding Maintenance Schedule
A well-structured maintenance schedule is your first line of defense against siding problems. This schedule provides a framework; adapt it to your specific siding type and local conditions.
Siding Type | Annual Maintenance | Bi-Annual Maintenance | As-Needed Maintenance |
---|---|---|---|
Vinyl | Cleaning with a pressure washer (low pressure setting), inspection for cracks or damage. | Detailed inspection for loose panels or signs of insect infestation. | Repairing cracks or replacing damaged panels. |
Wood | Cleaning with a soft brush and mild detergent, inspection for rot, insect damage, or loose paint. | Re-staining or repainting as needed, checking for warping or swelling. | Repairing or replacing rotted sections, addressing insect infestations with appropriate treatment. |
Fiber Cement | Cleaning with a pressure washer (low pressure setting), inspection for cracks or damage. | Detailed inspection for loose panels or signs of water damage. | Repairing cracks or replacing damaged panels. |
Aluminum | Cleaning with mild soap and water, inspection for dents, scratches, or loose fasteners. | Check for corrosion or signs of rust. | Repairing or replacing damaged sections. |
Common Siding Problems and Solutions
Understanding common siding issues and their solutions is essential for effective maintenance. Early detection and prompt action can prevent minor problems from escalating into major, costly repairs.
- Water Damage: Water intrusion can lead to rot, mold, and structural damage. Solutions involve identifying and sealing leaks, repairing damaged flashing, and ensuring proper drainage around the foundation.
- Insect Infestation: Termites and carpenter ants can cause significant damage to wood siding. Regular inspections and professional pest control are crucial. Treatment may involve insecticide application or replacement of severely infested sections.
- Cracks and Gaps: These can occur due to weather, settling, or age. Small cracks can often be caulked; larger cracks or gaps may require panel replacement.
- Loose or Damaged Panels: Loose panels can be a sign of underlying structural issues or simply loose fasteners. Re-fastening or replacing damaged panels is necessary.
- Paint or Stain Failure: For wood siding, peeling paint or faded stain indicates a need for repainting or restaining to protect the wood from the elements. Regular maintenance, such as cleaning and repainting every 5-7 years, is key to extending the life of the paint job.
Importance of Regular Maintenance
Regular maintenance is an investment that pays off handsomely in the long run. By addressing minor issues promptly, you can prevent them from escalating into costly repairs. For example, a small crack in vinyl siding, if left unaddressed, can allow water to penetrate, leading to rot in underlying wood framing – a much more expensive repair than simply caulking the crack.
A proactive approach to siding maintenance helps to extend the lifespan of your siding by many years, saving you significant expense and protecting your home’s value.
Regular maintenance is not just about aesthetics; it’s about preserving the structural integrity of your home.
Final Thoughts
Ultimately, choosing new siding is a significant investment, but with careful planning and the right information, it can be a rewarding experience. Remember, selecting the right materials, finding a reputable contractor, and understanding the entire process are key to achieving a successful and beautiful outcome. By following the steps Artikeld in this guide, you can transform your home’s exterior, enhancing its curb appeal and protecting it for years to come.
Don’t hesitate to ask questions and do your research – your dream exterior awaits!